Augmented Reality in the Transportation and Logistics Sector: Part 3
This is the third part of a five-part series covering the impact of Augmented Reality on the transportation and logistics industry.
In the first two parts of our new five-part series on Augmented Reality in the Transportation and Logistics sector, we looked at some of the overall business imperatives behind the many changes in this sector – as well as the specific challenges facing the trucking industry (and ways in Augmented Reality technology might help address them). We also looked at a very useful framework for thinking about the overall industry (offered in a recent report by strategy and analysis firm PwC).
Download our new Transportation and Logistics eBook
In this third part of the series, we’ll take a look at how logistics and transportation companies can go about assessing their needs for an AR solution (and calculating the Return on Investment it could provide). The good news is that the process for assessing need is pretty consistent across all parts of the transportation and logistics sector, whether you are talking about logistics services, air and express delivery services (EDS), freight rail, maritime transportation (including carriers, seaports, terminals, and labor involved in the movement of cargo and passengers by water) or trucking.
All these parts of the sector have one thing in common: they all rely on large, expensive and complex machinery to keep them going. Any time that machinery isn’t on the road, in the air, at sea, riding the rails – or underpinning the smooth running of warehouse operations – money is being lost.
The promise of Augmented Reality is to help ensure that industrial workers in all parts of the sector can get fast access to the remote experts, instructional content and collaboration tools they need to quick resolve any issues that are preventing a ship from leaving port, a plane getting in the air, a truck getting back on the road, a cargo train leaving the station or goods leaving the warehouse.
So the framework for thinking about Return on Investment starts right there. What does downtime cost?
To get a sense of just how downtime can cost, consider the results of a 2006 joint survey of 101 manufacturing executives in the auto industry by Nielsen Research and Advanced Technology Services (ATS) found that, at that time, the cost of stopped production was an average of $22,000 per minute (which comes to an eyebrow-raising $1.32 million per hour).
Suffice it to say that for some parts of the transportation and logistics industry today, that hourly downtime number would still be significant. Recall the comments made by Duke Drinkard, retired vice president of maintenance at Southeastern Freight Line and current president of the 21st Century Driver and Truck Alliance, in Part 2 of this series – where he discussed the very specific downtime costs created by repair delays for long-haul trucks.
He said that shortages of skilled and experienced long-haul trucking repair staff have translated to longer repair times for trucks. It has caused a lot of companies to see a rise from having to maintain a 5% contingency allowance (in terms of extra truck capacity to fill in when other trucks in a fleet are down) to needing a 15% contingency of extra trucks.
“Accurately calculating downtime should be a part of how you plan for AR – and think about the return on an AR investment. It’s where AR can really make a huge, measurable difference.”
So as you look at whether investing in Augmented Reality will provide the return on investment that you need, you may well be able to make that calculation based on the cost of downtime reduction alone. You need to start with a clear and accurate baseline for what it currently costs your enterprise to deal with downtime issues and – if possible – be able to break out cases where the cost of the downtime was significantly increased by not being able to get the right experienced person dealing with the issue in a timely way.
One great example of where this strategy was employed well comes from Porsche Cars North America. In November of last year, Porsche Cars North America, Inc. (PCNA) announced the introduction of “Tech Live Look,” an Augmented Reality technology designed to improve technical services at Porsche dealerships in the United States.
“Tech Live Look” uses our software platform, in conjunction with lightweight smart glasses, to create this solution.
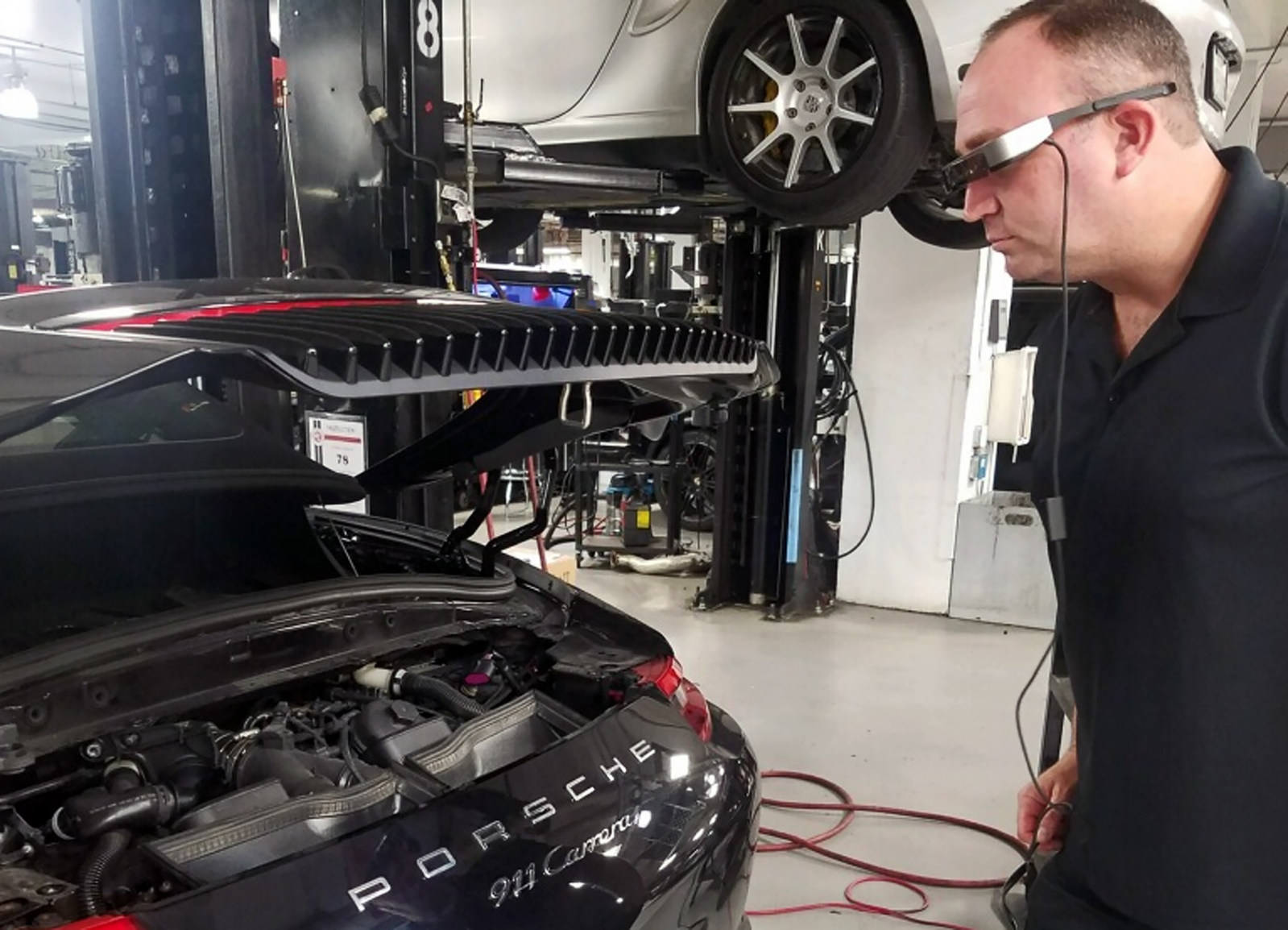
“Tech Live Look” allows Porsche dealership technicians to connect with the remote support team in real time. (PRNewsfoto/Porsche Cars North America, Inc.)
How does this technology work? When a service technician at a dealership in Los Angeles dons this specialized eyewear and connects through the software with the Atlanta-based Porsche technical support team 2,200 miles away, it allows the support team to see exactly what he is seeing, in real time.
This “see what I see” videoconferencing capability with instant access to remote experts allows both parties to quickly identify and resolve technical issues. Porsche did its homework on ROI and concluded that this AR solution can help decrease service resolution time by up to 40 percent, based on the findings of a pilot program undertaken in July 2017 at eight Porsche dealerships in California, Florida, Indiana, New Jersey, and Washington, along with one in Canada.
Next, in the fourth of our five-part series covering the impact of Augmented Reality on the transportation and logistics industry, we’ll take a look at best practices for planning and implementing an AR solution.
This article was written by Geof Wheelwright, a technology journalist for more than 25 years (including work for The Times of London, the Financial Times, Newsweek, Time Magazine, The Guardian and trade publications such as Computerworld and Geekwire) and is now the Director of Marketing Communications for Mountain View, California-based Atheer, Inc.