Status of the global manufacturing sector
The economy has always had a pivotal role inside societies that have evolved over centuries. In recent decades, we witnessed several industrial revolutions that have shaped our civilization [1]. One of the best examples of the role played by manufacturing in our society is the introduction of the assembly line by Henry Ford in 1913. Nowadays, in the midst of the fourth industrial revolution, new industries are being created and existing ones are being reshaped [2] following the status in the global manufacturing sector. The four industrial revolutions are described in Figure 1 below. Since the manufacturing demand and the needs of societies are closely related, business models and manufacturing systems have always adapted to the technological changes imposed by each industrial revolution [1].
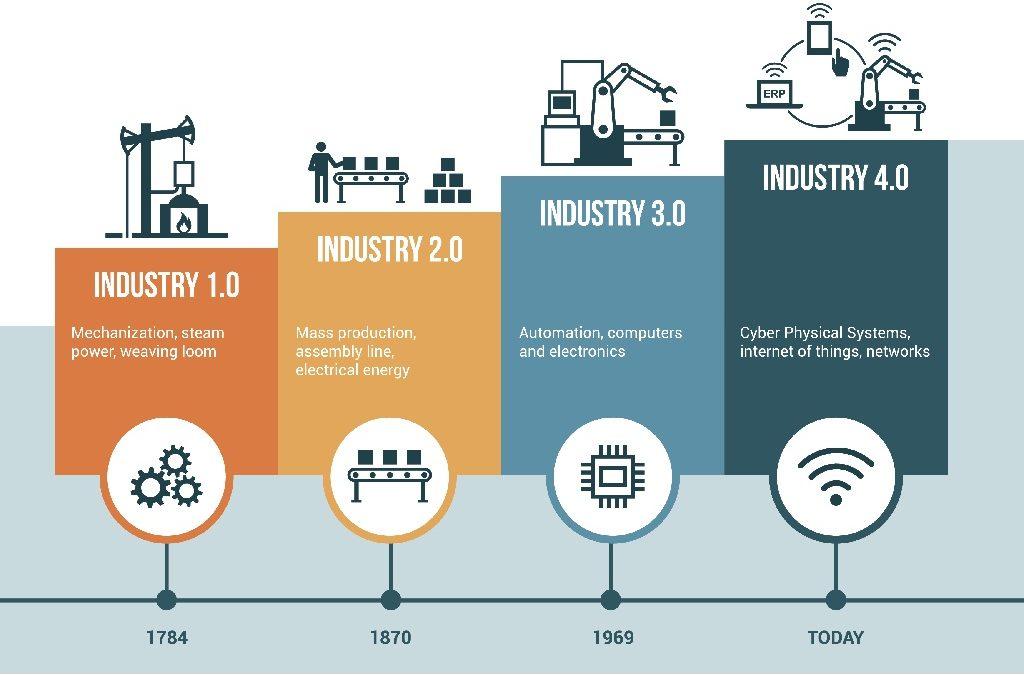
Figure 1. The four industrial revolutions
Status in the global manufacturing sector
Therefore, the manufacturing paradigm has evolved across centuries shaping the manufacturing process from a craft-based one that produced quasi-unique products, to a mass production environment and back towards a diversified and specialized production that better reflects the customer needs [1]. Figure 2 below shows this evolution.
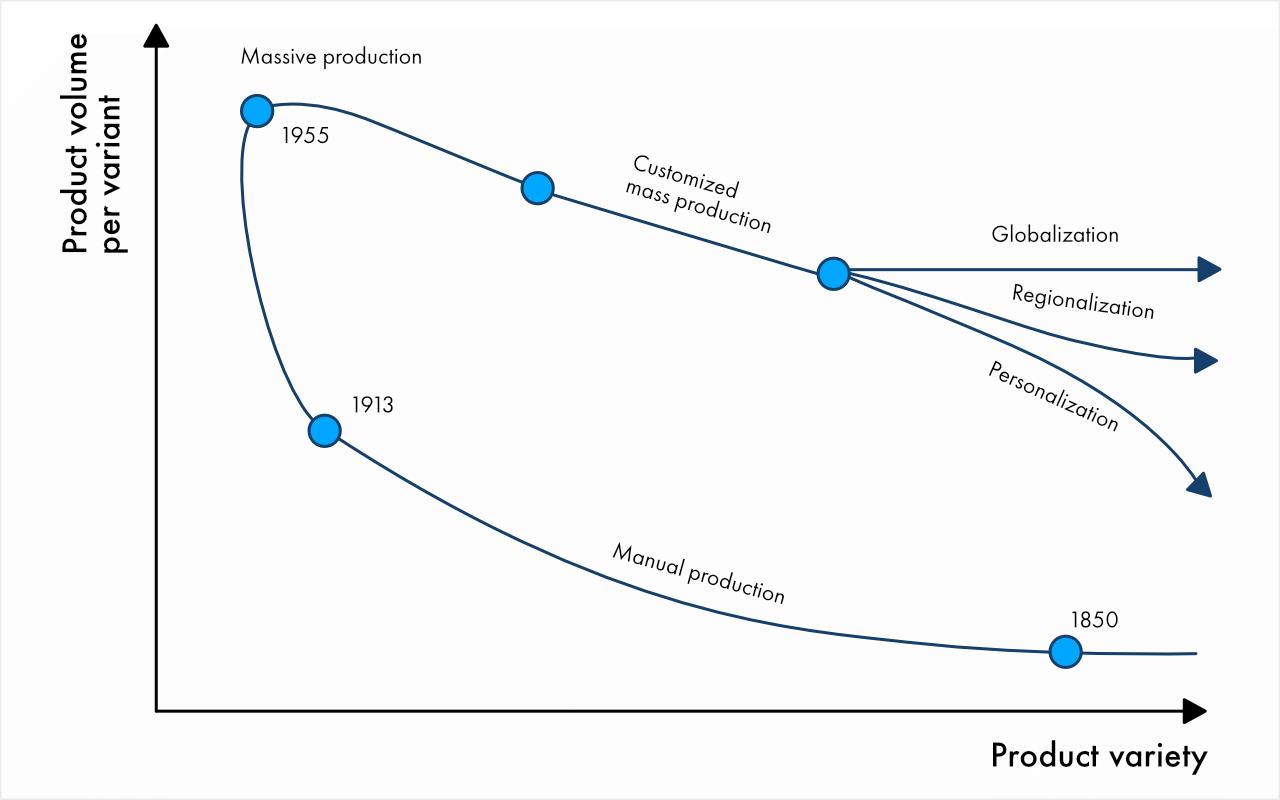
Figure 2. Evolution of production
However, adapting to the market and demand changes is not trivial and companies do not suddenly become more competitive just by acknowledging the trend. Manufacturing industries are currently under a lot of pressure from trends such as the globalization, trends that have been building up over the course of the years. In addition, as shown in Figure 3 below, manufacturing is considered to be the least value-adding step in the production process.
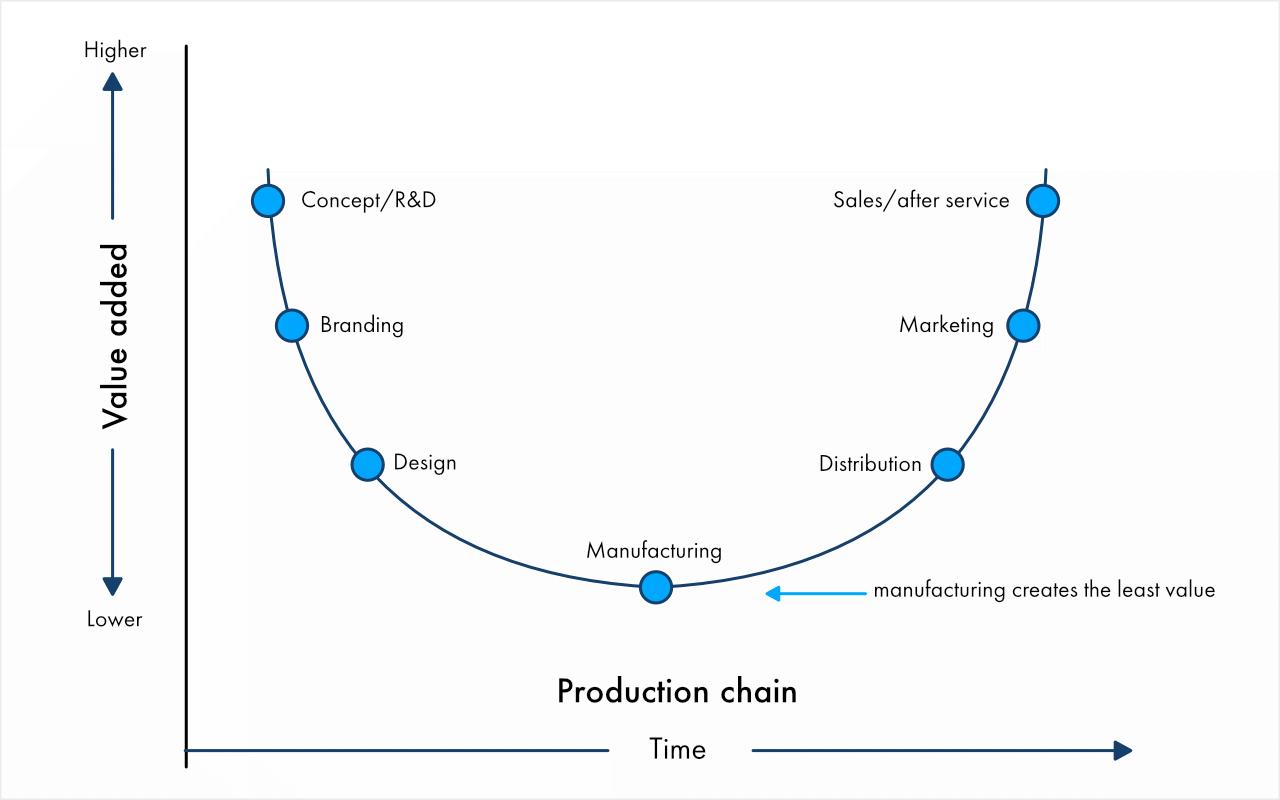
Figure 3. Smile curve of value added in production industries
More Manufacturing Trends 2022
The main purpose of this current Industrial revolution is to enhance the physical world with the help of the digital one for faster feedback and control loops throughout distributed manufacturing infrastructures.
The main status and challenges faced by manufacturing organizations:
- Customer expectations for increasingly complex and customized products and services
- Business model disruptions like “Manufacturing-as-a-Service” changing the value chain
- The rapid change from accelerating innovation cycles and time-to-market expectations
- Productivity plateaus in developed economies due to the lack of young, skilled labor force
- Regulatory pressure driving energy efficiency and pollution-reduction targets
- Rising input costs as population growth drives up labor, land, and raw material costs
- Globalization resulting in factories, vendors, and customers distributed across borders
As one industry leader formulated it in [1]:
“Stand-alone plants can also communicate with other factory sites, merging vast industrial infrastructures already in place with cloud computing and IoT. The end result is a complex but vibrant ecosystem of self-regulating machines and sites, able to customize output, optimally allocate resources and offer a seamless interface between the physical and virtual worlds of construction, assembly, and production.”
Future status of the manufacturing industries
According to 20th-century logic, the future of manufacturing industries would seem bright due to a constant population growth pushing the manufacturing industry into a quest for efficiency, reliability, seamlessness, and speed. 27% of global manufacturers estimate at least a 10% year over year increase in revenues for the next 5 years, while 30% of them estimate a growth between 5% and 10%. However, this growth does not come without challenges [5].
Moreover, companies in the manufacturing sector are quickly realizing that their Supply Chain Management (SCM) must become anticipatory, adaptive and environmentally aware, in order to cope with the new realities and achieve business sustainability. Furthermore, no individual company can optimize its own SCM without suffering from friction, waste from time lags, price arbitrage, and opacity. All these problems must be solved in the context of increasingly complex supply chains that operate in a rapidly changing environment [5].
In this case, survival of the fittest means that companies that are not adopting new technologies such as the Internet of Things (IoT), predictive analytics and blockchain will not be able to withstand the competitors that do so. Apart from an obvious improvement of efficiency, these technologies also increase transparency and manufacturing visibility of business operations faster than ever [5].
Recent studies estimate that the number of installed IoT devices will be growing from 15.4 billion in 2015 to 30.7 billion in 2020. The number of installed IoT devices will more than double in 2025 compared to 2020, reaching 75.4 billion The main growth drivers in IIoT are estimated to be applications such as fleet management, security applications, inventory and warehouse management as well as industrial asset management. All these applications are pushing for an increase in transparency and speed of transactions and processes in the supply chain [5].
Trusted supply chains, involving the onboarding of new suppliers through heavily scrutinized due diligence and compliance processes is an area in which manufacturing companies invest a lot of time and money nowadays. The reason for this is the need for alignment in terms of responsiveness to change in production needs, traceability of both raw materials and finished goods, anti-counterfeiting and Intellectual Property (IP) protection, all along the manufacturing supply chain. Investing in these exclusive solutions creates strong bonds between companies, but also centralizes the control of assets and networks [5].
Although these relationships provide a sense of security for businesses, this sense of security is usually as strong as the weakest firewall in the chain. Simply building stronger firewalls is a race against the horizon that shows the need for new, comprehensive enterprise solutions for security [5].
On the other hand, the Cybermanufacturing (CM) environment which comprises networked organizations and connected machines creates an opportunity for a fast transition of products between design and manufacturing. Product designs can be generated and then rapidly manufactured with little to no human intervention through automatic parsing and transfer of design data to machine instructions. The trust issue comes back into the discussion even in this Industry 4.0 scenario as several parties are still involved in the design, fabrication, production, sourcing, and verification of product assemblies. As explained above, trust is embedded in the supply chain via several activities such as contract negotiations, certifications, audits, etc. All these trust-building operations underwent by all parties of a supply chain of a product assembly determine the so-called “trust tax”, a cost that is embedded in the final price and passed on to the consumer [6]. More about Connected Manufacturing: What it is and Why it is Important
“Pull” based manufacturing platforms have proposed a partial solution for this trust problem. The digitalization and globalization have enabled the pull-manufacturing ecosystems, directly connecting end users with manufacturing capabilities. Operating with almost zero physical assets, the platforms add value to the end consumers, manufacturers, service providers, and other platform participants by acting as an information broker for all parties involved. Consumers trust these platforms to connect them with verified manufacturers and lower their sourcing cost, while manufacturers gain an additional sales channel. However, apart from the obvious downside of centralization and the fact that information is still opaque to a certain degree, these platforms do not make much sense in the context of highly regulated industries such as medical, military or aerospace [6]. Check our useful resources about the state of automotive, industrial & medical electronics manufacturing.
Even in “virtual” value chains, like the ones enabling 3D printing, the need for trust imposes uncertainty, cost, and delays. Apart from the need to protect the IP of original designs as they are being handled along the value chain, the associated parameters required for calibrating and operating the 3D printers need to be protected as well [7].
Moreover, customers need to know that the correct original design was referenced, the raw materials used are not counterfeited and are according to the specifications, machines worked properly and the Quality Assurance (QA) reports were generated, the parts were shipped and received on time, etc. Details about the payment need to be of course monitored and potential conflicts resolved. Finally, manufacturing partners need immutable records that validate and verify the ownership of their intellectual property, such as their proprietary manufacturing methods, as it moves along the value chain [7].
Further reading: A Guide to Machine Learning In Manufacturing
FAQs about the global manufacturing sector
How can IoT be used to improve manufacturing productivity?
IoT can improve manufacturing productivity by enabling real-time monitoring of equipment, predictive maintenance, efficient supply chain management, and data-driven decision-making, leading to reduced downtime and increased efficiency.
What are the applications of IoT in the manufacturing industry?
Applications of IoT in manufacturing include predictive maintenance, quality control, supply chain optimization, asset tracking, and smart manufacturing processes that leverage data from connected devices to enhance overall efficiency.
What are the five industries that can benefit from IoT?
Five industries that can benefit from IoT are manufacturing, healthcare, agriculture, transportation, and energy. These sectors leverage IoT for increased automation, data-driven insights, and improved operational efficiency.
What is a real-life example of IoT in manufacturing?
A real-life example of IoT in manufacturing is the use of sensors on production equipment to monitor performance and detect anomalies. This data is then analyzed in real-time to predict maintenance needs, reducing downtime and optimizing production processes.
Bibliography
[1] International Electrotechnical Commission, “Factory of the Future”(http://www.iec.ch/whitepaper/futurefactory/)
[2] VDI (The Association of German Engineers), ASME (American Society of Mechanical Engineers), “Industry 4.0 A Discussion of Qualifications and Skills in the Factory of the Future: A German and American Perspective” (https://www.vdi.de/presse/publikationen/publikationen-details/pubid/industry-40-a-discussion-of-qualifications-and-skills-in-the-factory-of-the-future-a-german-and/)
[3] Industrial Internet Consortium, “Smart Factory Applications in Discrete Manufacturing.”(https://www.iiconsortium.org/pdf/Smart_Factory_Applications_in_Discrete_Mfg_white_paper_20170222.pdf)
[4] “https://www.ibtimes.co.uk/mind-gap-industry-4-0-future-manufacturing-1665243”
[5] “https://www.coindesk.com/manufacturing-blockchain-prime-time-yet-come/”
[6] A. Angrisha, B. Cravera, M. Hasana, and B. Starly, “A Case Study for Blockchain in Manufacturing: “FabRec”: A Prototype for Peer-to-Peer Network of Manufacturing Nodes”, 2018, 46th SME North American Manufacturing Research Conference, NAMRC 46, Texas, USA (https://arxiv.org/pdf/1804.01083)
[7] B.BLECHSCHMIDT, DR. C.STÖCKER. “How Blockchain Can Slash the Manufacturing “TrustTax” ”(https://www.cognizant.com/whitepapers/how-blockchain-can-slash-the-manufacturing-trust-tax-codex2279.pdf)
This article was written by Radu Diaonescu, an electrical engineer by trade having earned an EPFL (Swiss Federal Institute of Technology Lausanne) Management of Technology masters and honed his skills while at Honeywell. He is currently managing Swie.io’s business development efforts and sits on the Board of Directors building the world’s next generation platform for agile manufacturing of electronics.