The actual cost of downtime in the manufacturing industry
For most manufacturers, downtime is the single largest source of lost production time.
What is Downtime in Manufacturing?
Downtime in manufacturing is any period of time when a machine is not in production (quite literally, down). Downtime can be categorized to help identify patterns in machine performance. It receives a high level of attention since equipment failures and breakdowns are highly visible.
However, as visible as downtime often is, most companies significantly underestimate their true downtime, and over 80% of companies are unable to calculate their true downtime costs correctly (“What is the True Downtime Cost (TDC)?” 2017).
To that end, not all downtime is created equal; in reality, the greatest expense is caused by unplanned downtime. Unplanned downtime is downtime that occurs unexpectedly or as a result of a failure (for example, a hardware failure or waiting for appropriate materials to complete a task). Common categories of unplanned downtime in manufacturing include excessive tool changeover, excessive job changeover, lack of operator, and unplanned machine maintenance.
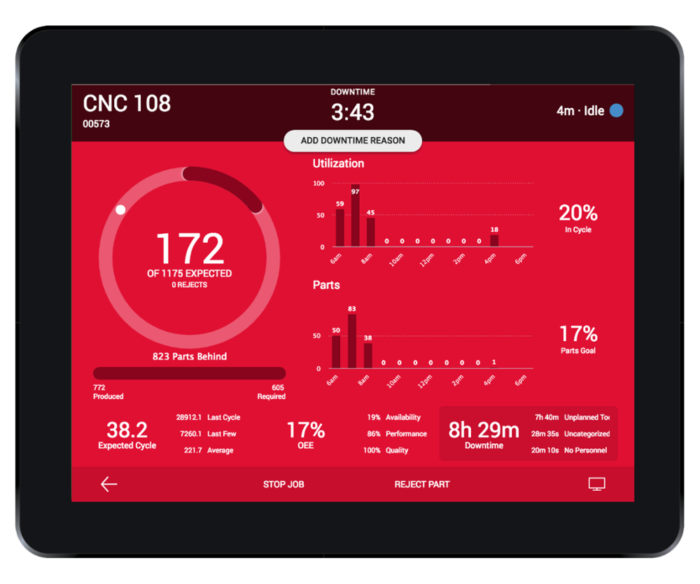
MachineMetrics notifies operators to add human context to machine downtime via tablets
The True Cost of Downtime in Manufacturing
A total of 82% of companies have experienced unplanned downtime over the past three years and that unplanned downtime in manufacturing can cost a company as much as $260,000 an hour! (According to Analyst firm Aberdeen Research). When unplanned downtime occurs, no value is being produced but the cost of overhead operations continues to grow, which directly impacts a company’s bottom line.
A new study sponsored by ServiceMax (conducted by Vanson Bourne of GE Digital), “After The Fall: Cost, Causes and Consequences of Unplanned Downtime,” surveyed 450 field service and IT decision makers across the Globe and in many industries including, manufacturing, medical, oil and gas, energy and utilities, and transportation. The study found that productivity, IT, and customer service are still hit hardest by unplanned downtime and that the reverberation is felt across businesses as a whole.
Unplanned Downtime Has A Great Deal of Costs
The same study also found that unplanned downtime is also driving renewed investment in digital transformation:
- Of the 82 percent of companies that have experienced unplanned downtime over the past three years, those outages lasted an average of four hours and cost an average of $2 million.
- Unplanned downtime results in loss of customer trust and productivity — 46 percent couldn’t deliver services to customers, 37 percent lost production time on a critical asset, and 29 percent were totally unable to service or support specific equipment or assets.
- Only 12 percent of respondents from organizations in the US consider their organization to be exactly where they need to be and ahead of their competitors in terms of their digital industrial journey — compared to 16 percent in both the UK and France and 23 percent in Germany.
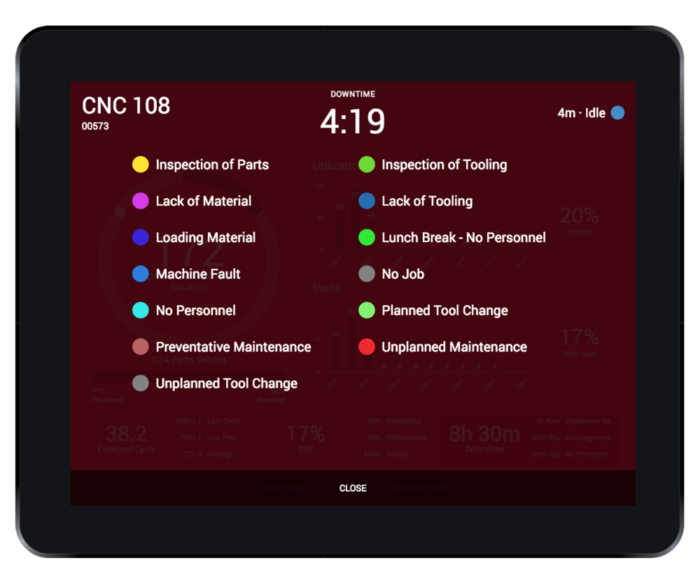
Customizable downtime reasons allow users to track planned and unplanned downtimes
Another startling statistic is that more than 70 percent of respondents aren’t fully aware of when their equipment is due for maintenance, upgrade or replacement. Even with the knowledge that unplanned downtime is so costly, manufacturers’ most frequently used approaches to maintenance—which should ideally help reduce unplanned downtime—are not necessarily effective in reducing it. A recent GE Study found that then only 24% of operators describe their maintenance approach as a “predictive” one based on data and analytics in manufacturing. The rest either took a reactive or time-based approach. In terms of the unplanned downtime associated with each approach, reactive approaches averaged 8.43% annually, with 7.96% for planned, and 5.42% for data/monitoring approaches.
Thus, the unplanned downtime Pareto is difficult to produce. It requires understanding all downtime that occurs on a machine, and not just the ones that we can gather through the machine’s PLC/Control. Traditionally, obtaining the necessary data involves log sheets that require the operator to manually log all significant downtime. This manual approach will likely miss frequent downtime events that are only a few minutes each but add up to a significant amount of time. Typically the actual data is logged well after the incident occurs, so the time is not very accurate. Utilizing a platform that tracks the cycle status of a machine in real-time is necessary to generate data for a downtime Pareto. It’s also necessary for the operator to categorize each downtime event into reasonable buckets during or shortly after an event.
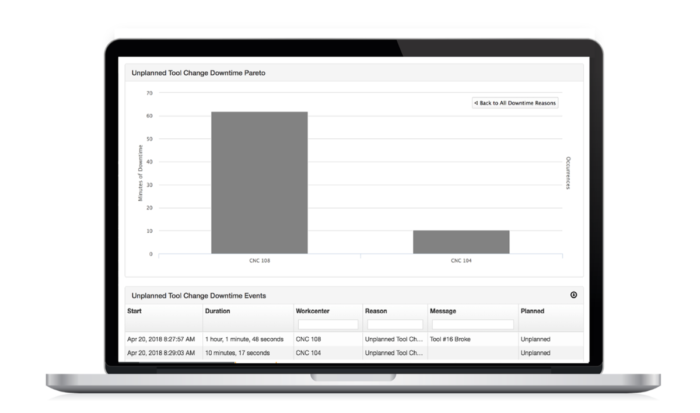
Downtime reports are visible by machine, job, shift, or operator for comparative analysis
The cost of one minute downtime in manufacturing
Unplanned work stoppages cost global industries millions of dollars in lost revenue. Downtime can be caused for multiple reasons. Examples can be weather delays in airline companies or cyber crime which lead to infrastructure breakdowns. Susceptibility to failure persists, particularly as it relates to factories. According to some research information, more than 90% of machines in plants globally are not network-connected, and the vast majority are more than 15-years-old.
Companies within the automotive industry are starting using Industry4.0 to develop data platforms designed to reduce downtime in an industry where every minute counts. Industry 4.0, or the Industrial Internet of Things (IIoT), refers to industrial manufacturing processes where all equipment, devices, and computers are connected. This creates an environment rich for big data analysis and self-correcting procedures, among many other possibilities.
This may seem like a far off future for manufacturers, but the truth is there are concrete examples of Industry 4.0 happening today. The capabilities of IIoT may be closer than people realize.
Causes of Unplanned Downtime in Manufacturing
Of course, while gathering data is a key driver in solving problems and having a better understanding of downtime, just obtaining more data does not mean that an organization will know what to do with it. According to a recent study by Accenture, 60% of operators cite dealing with outcomes of data gathered as a major challenge. It is important to understand the reasons for collecting increasing amounts of data and how the data can be applied to improve condition-based monitoring and predictive maintenance, including:
- The ability to identify data-based patterns
- Cognitive learning capabilities
- Opportunities to leverage data in the Cloud for cross-organization/industry comparisons
- The ability to share data with trusted service providers for additional analysis and insights
There is a significant opportunity to continuing carving down unplanned downtime through digitization, but as Deloitte notes in a recent report, “Simply ‘doing’ digital things will not make an organization digital.” Organizations need to go beyond just technology changes to truly embrace the benefits of digitization.
How Can We Prevent Downtime?
The first step to solving any problem is defining the problem. For downtime, knowing when, where, and how downtime occurs is essential to know how to prevent it. An early step toward reducing unexpected production backups or outright downtime can be achieved by carefully and accurately tracking when and where downtime occurs. The time is now to invest in the digital tools that will transform your business and the technology to drive continuous improvements into the next generation of manufacturing.
Further reading: Why 85% of Machine Learning Projects Fail – How to Avoid This
How to achieve the zero downtime solution
To achieve a great ROI in their manufacturing processes in their facilities, companies make use of different solutions such as monitoring techniques and software or predictive maintenance. Data captured from robots, tooling and other network-connected elements, indicates what is going to fail before it fails, allowing for downtime to be avoided, but also for maintenance to be performed only when it is necessary to production.
Another feature of ZDT (the zero downtime) is real-time process improvements. While this is not yet possible, once enough data is collected from robot performance, the goal is to create a system that diagnoses itself based on minute changes in processes, which can then be adjusted to boost overall efficiency.
Industry 4.0 provides as yet unforeseen benefits for manufacturers. Despite that fact, companies are pushing the boundaries of what’s possible in automation and implementing the future of Industry 4.0 today.
The Cost Of Downtime In Manufacturing – Conclusion
It’s a very simple equation. If your equipment isn’t working, neither are you. That’s why downtime is one of the biggest expenses incurred by any manufacturing operation. When your production line is stopped for any reason, it’s akin to watching your money burn. Not only do these interruptions often mean costly repairs, but they also force you to play catch-up. You start to miss your targets, resulting in overtime and making a dent in your reputation. Even a few hours of inactivity can cost you millions of dollars, not to mention the series of setbacks you’ll experience.
This is why it’s so crucial for manufacturers to be vigilant when it comes to the most common causes of shutdowns. These can include neglecting maintenance, running dated software and postponing equipment upgrades. Not every issue is directly related to machinery, however. In many cases, interruptions occur because employees aren’t sufficiently trained. Other disruptions can be traced back to managers who failed keep detailed records of past problems. These records could have been used to identify and address trouble spots before they could lead to a shutdown.
When it comes to dealing with downtime, an ounce of prevention is worth at least a pound of cure. Supervisors and managers need to be proactive. This means gathering as much data as possible and also performing a risk audit. Knowing exactly where something is likely to go wrong means you can take steps to keep that from happening. Preventative maintenance is one of the most important means of avoiding downtime, as is investing in proper training for your personnel. Hiring a third-party service provider can help you stay on top of everything you need to do.
Don’t let downtime ruin your productivity. For other tips on eliminating this threat from your processes, take a look at the accompanying guide.
Guide created by S. Himmelstein & Company a leading manufacturer of torque tranducers
More about Industry 4.0 new solutions for manufacturing
FAQs about the cost of downtime in manufacturing
What is considered downtime?
Downtime refers to the period during which a system, process, or equipment is not operational or available for its intended purpose. It often implies a pause in productivity due to maintenance, repairs, technical issues, or other interruptions.
How do you calculate downtime in manufacturing?
Downtime in manufacturing can be calculated by subtracting the total uptime (productive time) from the total time within a given period. The formula is: Downtime = Total Time – Uptime.
What is an example of downtime cost in manufacturing?
An example of downtime cost in manufacturing includes the expenses incurred due to halted production, such as lost revenue, missed order deadlines, increased labor costs during recovery, and potential penalties for delayed shipments.
What is the manufacturing industry standard for downtime?
The manufacturing industry standard for downtime can vary based on the sector and the specific process. It’s crucial for each manufacturing organization to define its own acceptable downtime limits based on production goals and industry benchmarks.
How do you calculate the cost of downtime in manufacturing?
The cost of downtime in manufacturing can be calculated by multiplying the downtime hours by the fully burdened labor rate and adding any other additional costs incurred during the downtime, such as lost revenue and material waste.
What is the standard machine downtime?
The standard machine downtime varies depending on the industry, type of equipment, and production goals. Organizations often aim to minimize machine downtime through preventive maintenance and efficient operations.
Read the full article here and more about MachineMetrics solutions here.
Graham Immerman is Director of Marketing for MachineMetrics, a venture-backed manufacturing analytics platform. Graham has quickly become an authority on digital transformation and the application of IIoT technology for the manufacturing industry. An accomplished leader and experienced start-up veteran with an integrated background in digital, social, traditional, account-based marketing, growth strategies, and business development.